OPERATIONS MANAGEMENT
CHECK POINT 72: OPERATIONS PLANNING
This Check Point Is Available By Subscription Only,
But You Can Still Check Out The Menu Below. |
|
|
DO I NEED TO KNOW THIS CHECK POINT?
|
|
OPERATIONS MANAGEMENT
CHECK POINT 72: OPERATIONS PLANNING
Please Select Any Topic In Check Point 72 Below And Click. |
|
|
DO I NEED TO KNOW THIS CHECK POINT?
|
|
WELCOME TO CHECK POINT 72 |
|
|
HOW CAN YOU BENEFIT FROM CHECK POINT 72? |
|
The main purpose of this check point is to provide you and your management team with detailed information about Operations Planning and how to apply this information to maximize your company's performance. |
|
In this check point you will learn: |
|
• What is operations planning?
• About principles and lean operational guidelines for operations planning.
• About aggregate planning in a manufacturing environment.
• How to prepare an aggregate production plan?
• About operations planning strategies for meeting non-uniform demands.
• About key factors in operations planning in a manufacturing environment.
• About two main functions of operations planning in a manufacturing environment.
• About production scheduling tasks and preparing a master production schedule.
• About work scheduling in a job shop and batch production environments.
• About work scheduling in a flow production environment. and much more. |
|
LEAN MANAGEMENT GUIDELINES FOR CHECK POINT 72 |
|
You and your management team should become familiar with the basic Lean Management principles, guidelines, and tools provided in this program and apply them appropriately to the content of this check point. |
|
You and your team should adhere to basic lean management guidelines on a continuous basis: |
|
• |
Treat your customers as the most important part of your business. |
• |
Provide your customers with the best possible value of products and services. |
• |
Meet your customers' requirements with a positive energy on a timely basis. |
• |
Provide your customers with consistent and reliable after-sales service. |
• |
Treat your customers, employees, suppliers, and business associates with genuine respect. |
• |
Identify your company's operational weaknesses, non-value-added activities, and waste. |
• |
Implement the process of continuous improvements on organization-wide basis. |
• |
Eliminate or minimize your company's non-value-added activities and waste. |
• |
Streamline your company's operational processes and maximize overall flow efficiency. |
• |
Reduce your company's operational costs in all areas of business activities. |
• |
Maximize the quality at the source of all operational processes and activities. |
• |
Ensure regular evaluation of your employees' performance and required level of knowledge.
|
• |
Implement fair compensation of your employees based on their overall performance.
|
• |
Motivate your partners and employees to adhere to high ethical standards of behavior. |
• |
Maximize safety for your customers, employees, suppliers, and business associates. |
• |
Provide opportunities for a continuous professional growth of partners and employees. |
• |
Pay attention to "how" positive results are achieved and constantly try to improve them. |
• |
Cultivate long-term relationships with your customers, suppliers, employees, and business associates. |
|
|
|
1. WHAT IS OPERATIONS PLANNING? |
 |
|
OPERATIONS PLANNING |
Business owners and operations managers must be fully familiar with all of the main elements of operations planning, which represent the foundation of all operational activities within every business organization.
Operations Planning is an integral part of an efficient process in every manufacturing and non-manufacturing company alike. In a manufacturing company, for example, this process entails systematic pre-determination of methods and procedures required for completion of products in the most cost-effective manner. In a service, merchandising, project or contract management company, this process similarly entails systematic pre-determination of procedures to accomplish specific tasks in the most cost-effective manner.
The main objective of effective operations planning is to ensure the most economical utilization of operational capacity, human energy, and material resources available in the facility. Operations planning is often a complex task and has to remain flexible enough to accommodate constantly changing requirements while manufacturing products or providing service, or managing a project or contract.
Note:
|
• |
The term "Operations Planning" is used in the context of a non-manufacturing or industrial service environment, e.g. electro-plating plant, packaging plant, automated dry-cleaning plant. This term is also used in the context of merchandising operations, i.e. wholesaler or retailer, and project or contract management operations. |
• |
The term "Production Planning" is used interchangeably with the term "Operations Planning" in the context of a manufacturing environment. |
• |
Additional information related to operations planning of Service Operations and Project And Contract Management Operations is provided in detail in Tutorial 4. |
• |
All information presented in this check point is based on traditional Western-type management approach. Lean Management is briefly introduced below and discussed in detail in Tutorial1. |
|
|
ADDITIONAL INFORMATION ONLINE |
|
|
|
2. PRINCIPLES OF OPERATIONS PLANNING |
 |
|
OPERATIONS PLANNING PRINCIPLES |
The three most common Operations Planning Principles are similar for most manufacturing and non-manufacturing companies alike as outlined below. |
OPERATIONS PLANNING PRINCIPLES
IN A MANUFACTURING ENVIRONMENT |
1. |
The production plan should include all products or groups of products processed by common manufacturing facilities. |
2. |
The production plan should be expressed in the simplest terms meaningful to the production employees. |
3. |
The production plan should conform to the prevailing world class operational guidelines for operations planning and control. |
|
|
OPERATIONS PLANNING PRINCIPLES
IN A NON-MANUFACTURING ENVIRONMENT |
1. |
The operations plan should include all types of service or groups of services processed by common service facilities. |
2. |
The operations plan should be expressed in the simplest terms meaningful to the service employees. |
3. |
The operations plan should conform to the prevailing world class operational guidelines for operations planning and control. |
|
|
COMPLEXITY OF OPERATIONS PLANNING |
Operations planning in a Job Shop and Batch Production environments is usually more complex in comparison with Flow Production since there is a much broader range of products and manufacturing operations.
Regardless of the manufacturing method, however, it is essential to ensure that the production output is carefully matched with a company's sales and financial budgets for a particular fiscal period. |
|
|
3. LEAN OPERATIONAL GUIDELINES FOR OPERATIONS PLANNING AND CONTROL |
 |
|
IMPORTANCE OF THE LEAN OPERATIONAL GUIDELINES |
To succeed in a highly competitive manufacturing or non-manufacturing environment alike, it is essential to take into consideration a broad range of Lean Operational Guidelines related to operations planning and control outlined below.
In order to accomplish this task, you and your management team must become familiar with Lean Management principles, methods, and guidelines contained in this program and apply them to plant layout. These guidelines have been developed by management experts in the Toyota Motor Corporation in Japan and contained in the Toyota Production System (TPS). |
MAIN ELEMENTS OF THE TOYOTA PRODUCTION SYSTEM |
|
Some of the Lean Operational Guidelines, based on Toyota Production System, related to plant layout are summarized below. |
LEAN OPERATIONAL GUIDELINES FOR OPERATIONS PLANNING AND CONTROL IN A MANUFACTURING ENVVIRONMENT |
1. |
Minimize equipment requirements for manufacturing and operational processes. |
2. |
Balance and synchronize all activities related to manufacturing and operational processes. |
3. |
Optimize manufacturing and operational cycles. |
4. |
Ensure level-loading of plant and machines in the production facility. |
5. |
Maximize the flexibility within the manufacturing facility. |
6. |
Reduce machine set-up times and change-over times within the manufacturing facility. |
7. |
Maximize the use of low cost automation for manufacturing and operational processes. |
8. |
Maximize the use of NC and CNC machines within the manufacturing facility. |
9. |
Eliminate machine-time and equipment waste in the manufacturing and operational processes. |
10. |
Eliminate labor-time and material waste in the manufacturing and operational processes. |
11. |
Maintain production planning based on shorter, but cost-effective production runs of smaller production lots. |
12. |
Maximize the use of U-Type machine cells for production planning purposes. |
13. |
Maximize the use of cross-trained operators for a broad range of manufacturing and operational processes. |
14. |
Minimize the production and operational lead times for product manufacturing. |
15. |
Identify and minimize all non-value adding operational activities, e.g. counting, checking, moving parts, preparing documents, packing, re-packing, and so on. |
|
Lean Management is discussed in detail in Tutorial 1. |
ADDITIONAL INFORMATION ONLINE |
|
|
|
4. AGGREGATE OPERATIONS PLANNING |
 |
|
AGGREGATE PLANNING IN A MANUFACTURING ENVIRONMENT |
The operations planning process in many companies starts with an Annual Manufacturing Forecast which considers overall operational requirements.
This type of planning, also known as Aggregate Planning, is designed to minimize the cost of meeting production demands by regulating three basic variables as illustrated below. |
THREE BASIC VARIABLES OF THE AGGREGATE PLANNING |
 |
|
 |
|
 |
Production Output Requirements |
|
Production Manpower Requirements |
|
Inventory Level Requirements |
|
|
ROUGH CUT CAPACITY REQUIREMENTS PLANNING |
One of the prime approaches frequently used in aggregate planning is a "bottom-up approach", or Rough Cut Capacity Requirements Planning. This approach prescribes formulation of operational plans for each product and subsequent summation of all individual requirements into an aggregate plan.
Operational Capacity Requirements Planning involves Material Requirements Planning (MRP) and estimation of equipment capacity requirements for a specified manufacturing period. Material Requirements Planning is discussed in detail in Tutorial 4.
A simplified example of an Aggregate Production Plan for a six-month period is illustrated below. |
ADDITIONAL INFORMATION ONLINE |
|
|
|
5. SMALL BUSINESS EXAMPLE
AGGREGATE PRODUCTION PLAN |
 |
|
AGGREGATE PRODUCTION PLAN |
ABC Manufacturing Company
Aggregate Production Plan For January 1, 2014 – June 30, 2014 |
Month |
Number Of Units – Product Line A |
Sold |
Manufactured |
Inventoried |
|
Year-End Balance |
|
|
50,000 |
January |
25,000 |
15,000 |
40,000 |
February |
20,000 |
10,000 |
30,000 |
March |
15,000 |
15,000 |
30,000 |
April |
25,000 |
20,000 |
25,000 |
May |
5,000 |
10,000 |
30,000 |
June |
30,000 |
15,000 |
15,000 |
|
|
|
6. OPERATIONS PLANNING STRATEGIES FOR NON-UNIFORM DEMANDS |
 |
|
OPERATIONS PLANNING STRATEGIES |
If the Production Demand remains steady during the fiscal period, operational planning becomes relatively simple. In reality, however, a company often experiences a non-uniform demand for products.
This, in turn, puts additional pressure on the production manager and further complicates the Operations Planning Process. It is necessary, therefore, to select effective strategies in order to meet a non-uniform manufacturing demand.
The Operations Planning Strategies, summarized below, may be implemented individually or applied in any combination depending upon the manufacturing operations. |
OPERATIONS PLANNING STRATEGIES
FOR MEETING NON-UNIFORM DEMANDS |
Method |
Cost |
Comments |
Strategy: Adjust The Manufacturing Rate In Accordance With The Fluctuating Demand. |
Work overtime and on weekends, if necessary, and maintain the existing number of employees. |
Cost of overtime and additional bonuses, if appropriate. |
Improved morale of some employees because of the opportunity to earn additional income. |
Employ additional employees on a permanent basis to accommodate peak demands. |
Cost of wages and benefits to underutilized employees during "slow" periods. |
Sometimes underutilized employees may be reassigned to other jobs during "slow" periods. |
Employ independent contractors or sub-contractors to complete a portion of work during the period of peak demand. |
Additional cost of independent contractors, and sub-contractors. |
Independent contractors and sub-contractors are not always as reliable as the employees who have been with the company for a long time. |
Examine the option of purchasing certain products instead of manufacturing them during the period of peak demand. |
The cost of purchasing additional products instead of in-house manufacturing may increase the overall production cost. |
The increased quantity of products purchased from outside suppliers may be cost-effective during the period of peak demand if it is planned in advance. |
Strategy: Absorb Demand Variations By Increasing Production, Adjusting Inventory Level, Or Shifting Demand. |
Manufacture additional product quantities for stock and hold to meet future increased demand. |
Additional cost of manufacturing and holding inventory in stock. |
This strategy is applicable only to product manufacturing companies. |
Develop special relationships with clients to optimize your manufacturing capacity. |
Minor cost related to additional effort of cultivating clients. |
This strategy is in accordance with the prevailing supply chain management guidelines. |
Increase your advertising and promotion efforts during "slow" periods. |
Additional cost of advertising, incentives, and discounts. |
This strategy is essential in a highly competitive market environment. |
Offer clients to deliver products earlier or later when additional manufacturing capacity is available. |
There is a possibility that some clients may not like such an idea and may go elsewhere if they don't get what they want. |
This strategy confirms again the importance of cultivating close relations between suppliers and clients. |
Strategy: Adjust The Number Of Employees In Accordance With The Production Demand. |
Employ additional employees on a temporary basis when the production demand increases. |
Cost of advertising, interviewing, hiring, and training of new employees. |
Sometimes it may be difficult to find suitable employees on a short-notice basis. |
Reduce working hours, cut overtime, and, if necessary, lay off employees during period of "slow" demand. |
Payroll cost reduction for remaining employees. Increased severance cost to employees who are laid off. |
This is a short-term policy, since it may cause a long-term negative effect and decreased morale and loyalty of employees. |
|
|
|
7. KEY FACTORS IN OPERATIONS PLANNING |
 |
|
OPERATIONS PLANNING FACTORS |
You and your operations management team must consider a number of important factors throughout the Operations Planning process in your organization. Some of the key factors related to operational planning are outlined below. |
KEY FACTORS IN OPERATIONS PLANNING
IN A MANUFACTURING ENVIRONMENT |
1. |
Production Materials.
Determining type, quantity, quality and availability of materials. |
2. |
Production Facilities.
Determining operational capacity, tooling, and availability of machinery and equipment. |
3. |
Production Methods.
Determining the most efficient procedure for each operation on each part of the product, specifying the auxiliary equipment, and grouping product parts into final assembly. |
4. |
Production Operations.
Determining the sequence in which operations must be carried out on each part of the product. |
5. |
Production Standards.
Determining the level of quality for each part in accordance with required specifications. |
6. |
Production Time.
Determining the time allowance for each operation in accordance with specified production methods. |
7. |
Production "Due Dates".
Determining dates for commencement and completion of each operation taking into account all factors mentioned above. |
|
|
|
8. TWO MAIN FUNCTIONS OF OPERATIONS PLANNING |
 |
|
THE PRIME PURPOSE OF OPERATIONS PLANNING |
The prime purpose of Operations Planning in a manufacturing environment is to provide answers to two important questions outlined below. |
TWO IMPORTANT QUESTIONS OF OPERATIONS
PLANNING IN A MANUFATURING ENVIRONMENT |
1. |
When can we schedule the manufacture of specific products or complete specific operations? |
2. |
Which plant or machine can we use to manufacture specific products, or complete specific operations? |
|
The answers on these questions represent the essence of operations planning in a manufacturing environment through its two main functions illustrated below. |
TWO MAIN FUNCTIONS OF OPERATIONS
PLANNING IN A MANUFACTURING ENVIRONMENT |
 |
|
 |
Production Scheduling |
|
Production Loading |
Scheduling of manufacturing processes into acceptable timetables. |
|
Loading various machines or operators in accordance with scheduled programs. |
|
|
|
|
9. PRODUCTION SCHEDULING |
 |
|
PRODUCTION SCHEDULING |
Production Scheduling is a planned allocation of manufacturing processes into an acceptable timetable within the production facility.
Production scheduling can be accomplished through use of a Master Production Schedule, which is in essence represented by a Gantt Chart. Henry L. Gantt was one of pioneers of scientific management.
A master production schedule, illustrated below, is usually prepared on a weekly, bi-weekly, or monthly basis, depending on the nature of manufacturing activities.
The scheduling of work facilitates a Short-Term Production Plan for various manufactured products, considering the production method, required quantities of materials, and labor force. The complexity of the Detailed Scheduling Task, also known as Shop Floor Control, depends upon the type of production method employed by a company.
The Scheduling Process starts by breaking the total assignment into a number of operations and selecting the most economical ways to accomplish these operations. In a manufacturing company, for example, production scheduling may entail several tasks outlined below. |
PRODUCTION SCHEDULING TASKS |
1. |
Identifying every component specified in the parts list or bill of materials. |
2. |
Checking the availability of appropriate drawings, tooling, materials, and labor. |
3. |
Checking the availability of operational capacity. |
4. |
Checking the existing scheduling requirements. |
5. |
Checking the necessity of placing purchase orders for all buy-outs, i.e. components or spare parts. |
6. |
Finalizing the selection of suitable sub-contractors. |
|
|
ADDITIONAL INFORMATION ONLINE |
|
|
|
10. SMALL BUSINESS EXAMPLE
MASTER PRODUCTION SCHEDULE |
 |
|
MASTER PRODUCTION SCHEDULE |
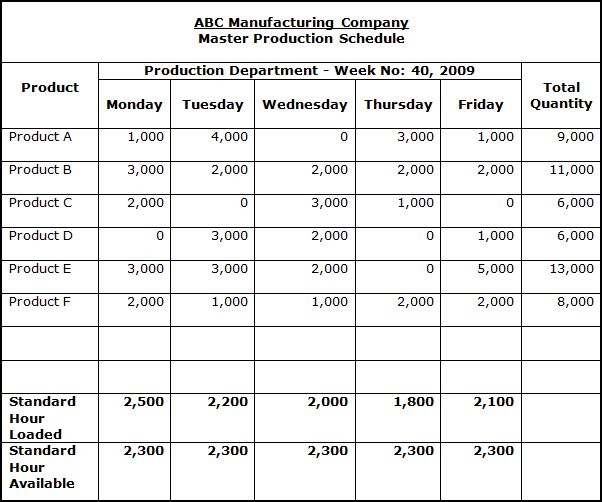
|
|
|
11. WORK SCHEDULING IN A JOB SHOP OR BATCH PRODUCTION ENVIRONMENT |
 |
|
SCHEDULING OF WORK IN A JOB SHOP OR BATCH PRODUCTION ENVIRONMENT |
The Scheduling Of Work In A Job Shop Or A Batch Production Environment entails summarizing individual manufacturing requirements into a Job Card. An individual Job Number must be allocated to every assignment handled in the job shop and a job card prepared accordingly.
Products manufactured in a batch production environment, on the other hand, can be identified by an appropriate Batch Number. Job cards for batch production are usually issued for every batch, or component, or operation depending upon the specific manufacturing requirements.
A typical Job Card is illustrated below. |
|
|
12. SMALL BUSINESS EXAMPLE
JOB CARD |
 |
|
JOB CARD |
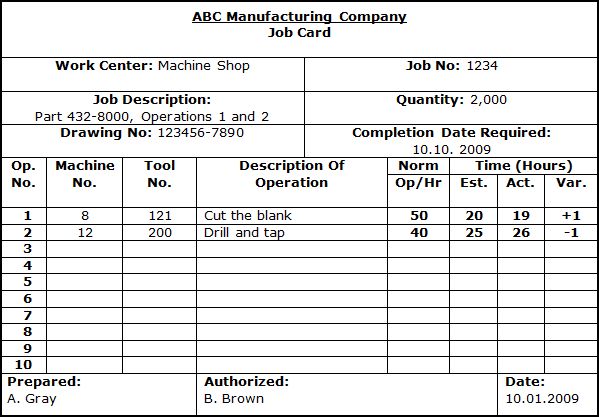
|
|
|
13. WORK SCHEDULING IN A FLOW PRODUCTION ENVIRONMENT |
 |
|
SCHEDULING OF WORK IN A FLOW PRODUCTION ENVIRONMENT |
The Scheduling Of Work In A Flow Production Environment requires a particularly high degree of accuracy since all operations are built into the manufacturing process.
Moreover, the Timing of each operation, or the Cycle Time, is of paramount importance, because the start of each following operation depends upon the successful completion of the previous one.
The Flow Production Process can be viewed as a long chain, where each chain-link is represented by a separate operation which is planned in advance to last one cycle time.
The cycle time for each operation must be 100% synchronized to ensure a smooth functioning of the entire process. Once the cycle time is out of balance, i.e. the synchronization is lost, the whole chain will be torn, i.e. the flow production process will be brought to a halt. The expression "The chain is as strong as its weakest link" has, therefore, a special meaning in the flow production environment.
Thus, it is absolutely essential to ensure that all elements, including appropriate drawings, tooling, and materials become available well in advance in accordance with Master Production Schedule requirements. If one of these elements is missing, the manufacturing process in a flow production environment may come to a complete stop, just like an interrupted conveyor production line. |
|
|
14. PRODUCTION SCHEDULING AND CONTROL SEQUENCE AND STEPS |
 |
|
PRODUCTION SCHEDULING AND CONTROL |
Many small and medium-sized manufacturing companies usually operate as Job Shops or utilize a Batch Production Method.
The sequence of Production Scheduling and Production Control for both methods is illustrated below. |
PRODUCTION SCHEDULING AND CONTROL SEQUENCE |
 |
|
 |
Job Shop Production Method |
|
Batch Production Method |
Step 1a: Receive customer's order and identify job requirements, i.e., specification, quantity, and delivery date. |
|
Step 1b: Receive customer's order and identify order requirements per product, i.e., specification quantity, and delivery date. |
 |
|
 |
Step 2a: Enter the job into the Job Order Book, allocate a Job Number, and prepare a Job Card/s. |
|
Step 2b: Combine similar product requirements from various customers into one batch, enter relevant details into the Job Order Book, allocate a Batch Number, and prepare a Job Card/s. If the product is a stock item, consider minimum inventory level requirements. |
 |
|
 |
|
Step 3: Check availability of drawings, tooling, raw materials, bought-out components, operational capacity, labor, and sub-contracting services for each job or batch. Refer to Bill Of Materials and Parts List.

Step 4: Authorize preparation of drawings, withdrawal from stores or purchase of tooling, raw materials, components, and sub-contracting services. Confirm prices and delivery dates.

Step 5: Schedule each operation specified in the Route Sheet. Enter relevant details into the Master Production Schedule considering the expected availability of drawings, tools, raw materials, bought-out components, operational capacity, labor, and sub-contracting services.

Step 6: Load operational capacity and utilize labor in accordance with Master Production Schedule requirements when relevant drawings, tools, and raw materials become available.

Step 7: Dispatch drawings, tools, and raw materials to appropriate working stations and issue relevant job cards in accordance with the Master Production Schedule requirements.

Step 8: Expedite overall control of all manufacturing activities and ensure that work is progressing in accordance with the Master Production Schedule requirements. Always maintain strict quality control.

Step 9: Prepare the necessary components for final assembly and ensure that all finished goods are properly inspected prior to storing them in the finished goods stores or dispatching them to customers. |
|
|
15. WEEKLY PRODUCTION SCHEDULING |
 |
|
WEEKLY PRODUCTION SCHEDULING |
Among the most important tools for production scheduling is graphical display of work allocation in various work centers. Such a display, or Weekly Production Schedule, provides an effective indication of Workload Status within the operations department on a weekly basis. This schedule, based on a Gantt Chart presentation which was discussed earlier, is illustrated below.
Each Job Number or Batch Number must be entered into the Weekly Production Schedule prior to the commencement of operational activities. This schedule can subsequently be used to show the duration and sequence of specific jobs that are scheduled for each individual work center. |
|
|
16. SMALL BUSINESS EXAMPLE
WEEKLY PRODUCTION SCHEDULE |
 |
|
WEEKLY PRODUCTION SCHEDULE |
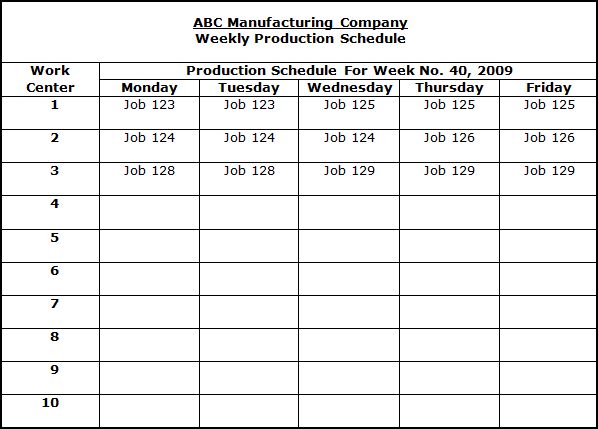 |
|
|
17. PRODUCTION LOADING |
 |
|
PRODUCTION LOADING |
Finally, when the Production Master Schedule is completed, the loading of work may begin.
The prime purpose of Production Loading is to allocate the existing workload to various machines and to ensure maximum utilization of available operational capacity and manpower resources in accordance with the existing production scheduling requirements.
Production loading is normally carried out on a daily or weekly basis depending upon the specific production requirements. The loading of each machine depends upon the availability of drawings, tooling, operators, and materials for every job. If materials are available early, they must be held in an appropriate material control area until the job is released to the work center.
Many manufacturing companies use a computerized version of Material Requirements Planning, called MRP and MRP II. These systems may require substantial financial investment, however, they often become cost-effective in a relatively short period of time and enable the company to remain profitable in a highly competitive market environment.
Material Requirement Planning (MRP) is discussed in detail in Tutorial 4. |
|
|
18. FOR SERIOUS BUSINESS OWNERS ONLY |
 |
|
ARE YOU SERIOUS ABOUT YOUR BUSINESS TODAY? |
Reprinted with permission. |
|
19. THE LATEST INFORMATION ONLINE |
 |
|
|
LESSON FOR TODAY:
Ignore People Who Say It Can't Be Done!
Elaine Rideout
|
Go To The Next Open Check Point In This Promotion Program Online. |
|
|